Instructions for use of cryogenic insulated gas cylinders (Dewar tank)
10/12/2023Instructions for use of Dewar tank
Dewar tanks are stainless steel pressure vessels with super vacuum insulation designed for the storage, transport and use of liquid oxygen, liquid nitrogen, liquid argon or carbon dioxide.These containers are manufactured to DOT4L standards for the reliable and economical transport and storage of cryogenic liquid gases, as well as for the on-site storage and supply of cryogenic liquid gases over a wide range of applications.
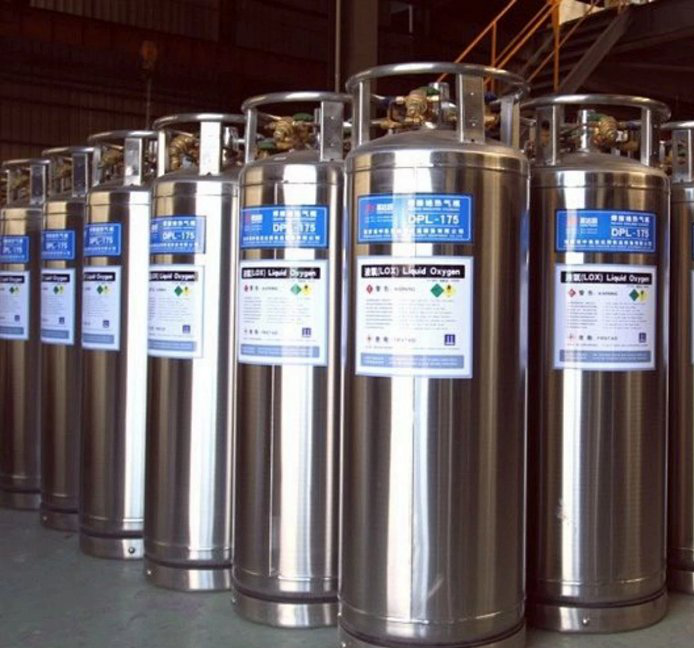
The structure of the Dewar tank
Dewar tanks generally have four valves, and the pipe in which the valves are located has a listed English logo. LIQULD stands for liquid use valve, USE (GAS USE) stands for gas use valve, VENT stands for venting valve, and (PBPRESSUREBUILD UP) stands for booster valve. As a rule of thumb, a small number of Dewar tanks don’t have gas use valves. In addition to this, there are gas phase pressure gauges and level gauges.
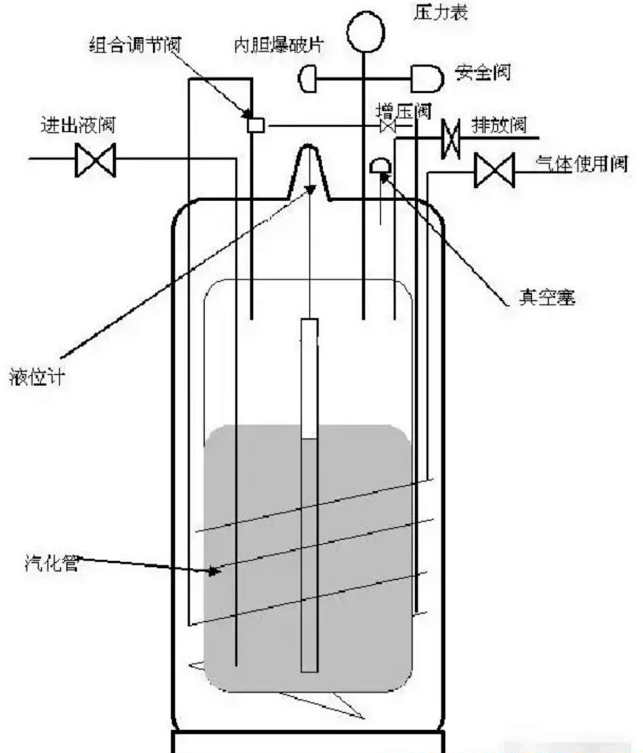
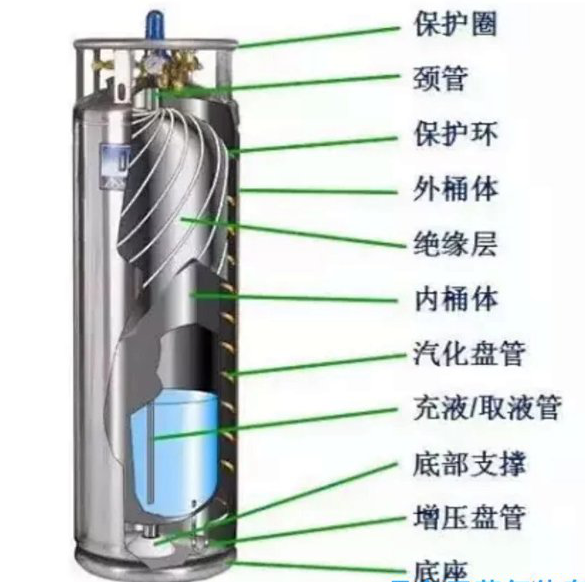
Use of Dewar tank
Generally, the liquid phase of Dewar can is used. The first step in using a Dewar tank is to connect the pipe where the Dewar tank liquid valve is located to the evaporator with a high-pressure metal hose, and the liquid use valve can be opened after confirming that it is connected, if the gas pressure does not meet the use requirements, open the pressure booster valve, wait a few minutes for the pressure to rise, and meet the use requirements can be used. When the Dewar tank has no liquid phase and the pressure of the gas phase is only 5kg, it means that the gas in the Dewar tank has been used, please close the liquid use valve and stop using it.
Advantages of Dewar tank
- Safe and reliable to use, easy and fast liquid discharge, low daily evaporation rate loss of static liquid.
- Compared to compressed gas cylinders, it is capable of holding large amounts of gas at relatively low pressures.
- It provides an easy-to-handle cryogenic liquid source.
- Due to the robustness and reliability of the Dewar tank , the long holding time, and the gas supply system itself, the built-in vaporizer can continuously output room temperature gas with a flow rate of up to 9.2m³/h, and the maximum constant output pressure of the gas is 1.2M Pa (medium pressure type)/2.2 M Pa (high pressure type), which fully meets the normal gas requirements.
- Set up multi-level safety protection device, better safety, and simple and reliable operation.
- Large storage capacity, can reduce storage space, reduce bottle changing operations, improve work efficiency.
- It avoids the quality hidden dangers caused by the fact that the cylinder gas is easy to suffer from secondary pollution due to many links during filling, transportation and use.
- High gas utilization: the cylinder gas must have residual pressure after each use, and the liquid gas supply can avoid any waste and reduce the cost of gas.
Operation method of Dewar tank air supply
[Preparations]
- Dewar tanks and cylinders should be kept at a safe distance.(The distance between the two tanks should be maintained at least 5 meters)
- There is no open flame device around the tank, and there should be a fire prevention device nearby.
- Check whether the Dewar tank is well connected to the end user.
- Check all valves, pressure gauges, safety valves in the system, the fixtures of the valves used in the Dewar tank should be complete and easy to use.
- The gas supply system shall not have grease and leakage.
[Operating procedures]
In order to make the Dewar tank gas supply system continuous, smooth, safe and economical air supply,when the Dewar gas supply system is used, a single Dewar tank can supply gas to the terminal, or two Dewar tanks or more than three Dewar tanks can be alternately switched by confluence.Please follow the steps below:
- Before connecting the hose, a part of the gas is released from the gas pipe system, and the air in the hose is removed and then connected to the interface of the Dewar tank to measure the flow rate of the production gas,Large quantities should be connected to liquid inlet and outlet valves (LIQUID) and small quantities should be connected to gas outlet valves (VENT).
- When the supply pressure is insufficient during use, open the booster valve to increase the pressure, and adjust the pressure regulator to automatically control the pressure boost range.
- When the liquid or gas flows out, the booster pipe, exhaust pipe, valve, etc. will be cooled and refrigerated, and the valves and joints may have air leakage, at this time, tap water should be used to shower, and then tighten the joint.
- The maximum pressure of the liquid tank is 12Kg/cm², beyond this pressure the safety valve will automatically exhaust, at this time the booster valve should be closed, and then opened after the pressure drops part.
- During use, it is not allowed to touch the ventilation hose, booster pipe, tank, etc. with your hands to avoid cold injury, and it is not allowed to knock on valves, pipelines, etc., so as to avoid embrittlement and rupture.
- When used, the liquid tank should be upright, not allowed to lie down, and when operating the valve, the operator is not allowed to face the positive direction of the valve discharge(Including the discharge direction of the safety valve).
- If the production of liquid discharge valve (LIQUID) needs to interrupt the gas supply halfway, after the discharge valve is closed, it is not allowed to immediately close the absolute check valve on the gas pipeline, because the liquid gas conversion gas in the metal hose cannot flow after rapid expansion, and an explosion injury accident will occur.
- After the operation is over, or after the liquid in the tank is used up, first close the booster valve, then close the inlet valve (inlet and outlet valve) of the Dewar tank, and remove the joint connected with the metal hose and the Dewar tank after emptying the liquid through the venting valve.
[Steps for emergency stops]
When an emergency occurs in the system or workshop and the gas supply system needs to be stopped urgently, the stop should be followed by the steps below.
- Quickly close the Dewar tank valve and booster valve.
- Quickly open the combined discharge valve.
- Quickly turn on the ventilation unit in the operator room.
[Notes]
- When the Dewar tank is not used in storage, remember not to open the booster valve, be sure to check whether the booster valve is closed, otherwise it will cause gas leakage in the tank.
- After stopping use, you must remember to close the open booster valve, the booster valve is only opened when it is in use.
- When the booster valve is fully opened, the pressure drop of the Dewar tank pressure gauge is no longer increased, which means that there is no liquid phase in the tank only the gas phase, and the gas phase pressure shall not be less than 5kg.
- Check whether there is air leakage at each connection (dynamic and static sealing point) during use, frosting during use is a normal phenomenon, and it is easy to be confused with Dewar tank air leakage.
- When the system pressure after the booster valve is opened, the system pressure shall not be greater than the pressure specified in the design, when the system pressure is too high, the pressure booster valve can not be controlled, the venting valve should be quickly opened to relieve the pressure of the system, and the reason can be put into use again after finding the reason.
- Check the pressure of the Dewar tank, try to check it every half an hour, when the pressure of the Dewar tank is low, the system booster valve should be properly opened or opened to increase the pressure of the system and avoid low liquid level.
[Additional considerations]
- When working with cryogenic liquids, it is essential to wear protective equipment to prevent frostbite.
- In the operation of liquid oxygen, the opening and closing of the valve should be carried out slowly, and the sudden opening and closing, the oxygen flow will cause any pollution in the system to catch fire.
- With the exception of liquid oxygen, all liquid vapors can suffocate people.
- When working with liquids, it is recommended to keep the pressure in the bottle as low as possible.
- During operation, the gas cylinder must be kept upright, and overturning should be avoided, and the cylinder should not be rolled horizontally.
- Open flames are strictly prohibited within 5m around the storage, vaporization, filling and use of liquid oxygen, all fire sources are eliminated, and there should be obvious fire prohibition signs.
- The storage, vaporization, filling and use of liquid oxygen is not allowed to have openings leading to low places (such as basements, pits, wells, ditches) within at least 5m; There must be a retaining weir at the entrance to the gutter.
- When filling or handling liquid oxygen, operators must not wear grease-stained overalls and personal protective equipment, and all grease-stained clothing and protective equipment must be replaced.